About Me
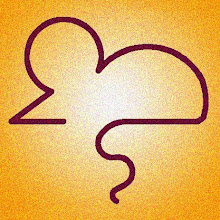
- Kelly's Studio
- Based in Northampton, UK, I live with my husband Adam, our Cocker Spaniel Bruno and Deeley the Bengal cat. I work full time as a Creative Artist / 3D Designer and part-time with my creative endeavours. I hope you'll enjoy reading about my work and other random ramblings, from the satisfying successes to the catastrophic failures! Still, it's all good fun, which is kind of the whole point really...
Wednesday, 26 March 2008
And the Winner Is...
Wednesday, 19 March 2008
COMPETITION!

The first casts
Below is the reverse of that model. Taking notes like this makes future casting much easier to plan, this one shows I used 45ml of resin, that it weighs 44g and that I used no filler. I planned to use filler on future copies (filler is powdered marble and reduces the curing temperature slowing it down so the model doesn't shrink so much) but as it makes the mixture cloudy (it's clear and slightly straw-coloured before curing) it makes bubble-checking more difficult, and I've not found any shrinkage issues so far so may not go that way.
This is the second copy I took from the mold, this one has no faults in it (apart from a bit of fluff that made it's way into the mix) which proved that the first "reference model" was in fact very effective. I'm so pleased that I can get a bubble-free copy of this awkward and challenging sculpture!
Finally, this is the 5th copy I got from the mold, I decided to experiment and see how bronze would act in PU (polyurethane) resin - I've always used PE (polyester) resin for Bronze casting but was advised that using PU resin would be ok. I did start to polish it up, you can see the beginnings of the shiny polished bronze on the lower horse's nose.
This is the back view of the same Bronze model. As you can see it is almost white - this is because bronze is much heavier than resin, so it quickly sinks. This gives a good colour to the front surface of the model, but does make the rear surfaces quite ugly - you can see the ear of one of the horses in this picture, and the rear surface of that is almost white too. When I started polishing the rest of this model a few issues arose with the finish too, so all in all I don't feel this method is a success, and I will be reverting back to using PE resin for all metals in the future.
You can see the notes on the back of this one too, I was conservative with the bronze on this test copy and used just 10ml by volume. Now 10ml of Bronze weighs over 100g so if that was measured by weight the mix would actually be under 40g of resin to over 100g of Bronze (which is 2:5 resin:bronze ratio by weight), normally I would use around 160g with a model of this size (1:4 resin:bronze ratio by weight!) but I don't feel that would have helped with the state of this one using the PU resin.
Friday, 14 March 2008
New medallion!!!
This is the mold, it's currently sat on my desk here at work (it had to cure overnight and I couldn't wait until later tonight to see if it had worked so brought it to work with me - impatient as ever!), though to be honest silicon is quite smelly so I don't think my colleagues appreciate it much!
So next up, tonight I will test out the new mold and take a couple of casts from it, hopefully it has worked well and I will be able to de-mold without damaging the casts (the undercuts are something else on this piece), I'll post more photos as I get copies!
Details on the competition to follow too!
Ingredients for a productive weekend!
An exciting day! I love receiving parcels, but today's didn't contain a resin horse (for a change!), it contained a bunch of materials for a weekend of mold-making and casting!
From left to right, there is:
- PU Resin (I'll keep it wrapped until I get home from work, for safety)
- Filmoront Acrylic Sealer
- Ormoline Sealer
- Powdered Brass
- Powdered Bronze
- Powdered Copper
- Powdered Aluminium (dangerous stuff - must be kept dry)
- Liquid Leaf in Rennaisance Gold
- 50ml and 30ml mixing beakers
- Wooden Tongue Depressers (mixing sticks)
- PE Resin (Keeping that wrapped until I get home too)
- In the background are a few of the orchids I have at work, I have 12, hehe!
A little info on all these ingredients:
- The PU Resin is used to create regular "unpainted resin" copies, it has a creamy white colour and is very slightly flexible which protects it from chips and cracks. It cures very quickly and gets very hot during curing, sometimes I add marble dust or synthetic onyx powders to part A and part B before mixing the two together which slows don the process, making less shrinkage and less heat which saves the mold. Adding the powder actually makes the resin a touch less "plastic", so paint adheres more easily to it.
- Filmoront Acrylic Sealer - this is a new one for me to try out, I'm going to try both this and the Ormoline Sealer on my cold-cast metal models, to see if I can keep the initial "shine" to them, as usually cold-cast metals do tend to dull after a short period.
- Ormoline Sealer - as above, I plan to use this on cold-cast metals. Ormoline is a mix of resin and solvent, so once it is painted on the solvent evaporates leaving a film of resin behind. I'm curious to see what effect this has on the finished models.
- Powdered Brass
- Powdered Bronze
- Powdered Copper
- Powdered Aluminium - these powders, when mixed with resin prior to pouring, then polished carefully, come up to a finish that has the feel, weight, temperature and look of real foundry cast metal.
- Liquid Leaf in Rennaisance Gold - I was thinking it'd be quite interesting to use this for adding gold accents to various resin finshes (slate etc), and also to add another angle to the cold-cast metals. I fancy making up a copper model, then painting the mane with this gold-leaf effect paint and then polishing it back.
- 50ml and 30ml mixing beakers - I use so many of these things - at least one per casting. For mixed finish models I can se as many as 5 or 6 of these handy little beakers. They aren't too expensive at about 25p (50¢) each, but I get through so many that they are a cost consideration when I price my models.
- Wooden Tongue Depressers (mixing sticks) - at just 2p (4¢) each these are much more affordable! These get used ofr mixing, for levelling out molds when they are uneven, and for many other uses.
- PE Resin (Keeping that wrapped until I get home too) - I use PE resin for cold-cast metals, as it is a one-part resin that you cure by adding a few drops of catalyst to, it's much easier to mix the metal with the resin (metal is VERY heavy so sinks quickly, making a two-part mixture difficult to mix together fully before it starts to cure). It is a touch more brittle than the PU resin though is still tough, and with the added metal it does come out very tough. I do plan to experiment with using PU resin for cold-cast metals (it would mean I only need one mold, not one for PU and one for PE, which is a benefit) but for now I'm sticking with what I know.
- This weekend I have plans - my entry for the RESS BAS Relief sculpture competition is very nearly complete, I'm hoping I can have it finished by tonight so I can take the first mold - I made an error on the placement of the model to the background, it needs adjusting so I will make a resin copy of the sculpture, then put that onto a new background before taking a mold of that for the final copies.
- I have an order for a copper Frodo to make, so as I've had to buy in metal for that I went ahead and bought brass, bronze and aluminium too, and I now have plans to make up a cold-cast metal copy of my model too, for the RESS competition Metals section.
- So, if all goes well, I should end the weekend with at least one metal Frodo (I also need to make up a couple for donations that are very late!); at least a couple of resin copies of the new medallion, one to paint up for the painted section of the competition too; and possibly a complex (mixed) metal copy of the new medallion.
- I'm going to be needing a name for this new medallion, I feel a competition coming on...!